What is Cement?
Cement is a binding agent, a substance used for construction that sets, hardens, and adheres to other materials such as stones, bricks, tiles, etc. and binds them together. It is the main component in construction thus making it the most widely consumed commodity after water. The extraordinary diversity of its uses makes it the material of the 21st century. Due to its importance and properties, most countries manufacture their own cement locally.
How is Cement Made?
Cement generally refers to a very fine powdery substance chiefly made up of limestone (calcium), sand or clay (silicon), bauxite (aluminium) and iron ore, and may include shells, chalk, marl, shale, clay, blast furnace slag, or slate.
Cement manufacturers mine materials such as limestone, shale, iron ore, and clay, crush and screen the rock, and place it in a cement kiln. After being heated to extremely high temperatures, these materials form a small ball called “Clinker” that is very finely grounded to produce Cement. Cement mixed with water causes a chemical reaction and the paste sets and hardens to bind sand and gravel together.
Lime and silica make up about 85% of the ingredients of cement. Other elements include alumina and iron oxide. The rotating kiln that cooks the materials resembles a large horizontal pipe with a diameter of 10-15 feet and a length of 300 feet or more. One end is raised slightly. The raw mix is placed in the high end and as the kiln rotates the materials move slowly toward the lower end. Flame jets at the lower end heat all the materials in the kiln to high temperatures that range between 2,700~3,000º Fahrenheit. This high heat drives off, or calcines, the chemically combined water and carbon dioxide from the raw materials and forms new compounds (tricalcium silicate, dicalcium silicate, tricalcium aluminate and tetracalcium aluminoferrite).
For each ton of material that goes into the feed end of the kiln, 2/3 of a ton comes out the discharge end, called clinker. This clinker is in the form of marble sized pellets. The clinker is very finely ground to produce Portland cement. Manufacturers often add gypsum and/or limestone during the grinding process.
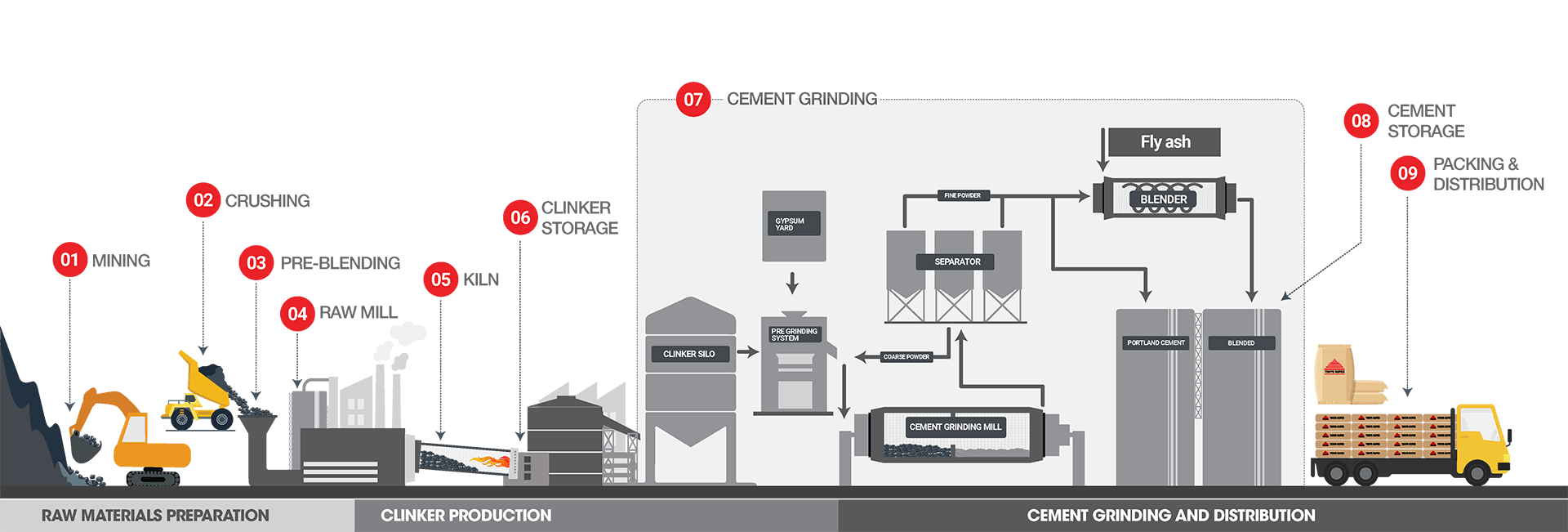
01 Mining
Limestone and clay are extracted using drilling and blasting techniques
02 Crushing
The quarried material is reduced in size in crushers by compression on impact.The crushed raw material is transported to the cement plant, using conveyors or rail wagons.
03 Pre - Blending
The limestone, clay and alternative raw materials such as silica stones, iron oxide, are mixed and homogenized. Baghouse filters of electrostatic precipitators remove particles from kiln and exhaust gases.
04 Raw Mill
The homogenized raw materials are ground and dried in a mill. The raw material is preheated before entry into the kiln
05 Kiln
Powdered raw materials are heated and sintered inside a kiln to produce cement clinker. At flame temperatures up to 2,000°C and materials temperature up to 1,450°C, the raw materials are transformed into clinker minerals.
06 Clinker Storage
The sintered clinker are quickly cooled down in an air quenching cooler. Cooled clinker is stored in silos in preparation for shipping or grinding.
07 Cement Grinding Mill
Cement clinker is ground with Gypsum and other cementitious materials to form the final cement types. Portland cement is made by granulating finely crushed cement clinker and Gypsum, in a grinding mill. Blended cements are produced by blending Portland cement and fly ash and other admixtures.
08 Cement Storage
Ground cement is stored in large storage silos.
09 Packing and Distribution
Cement is transported in bags or shipped as bulk cement.
How Does Portland Cement Absorb Water?
This chemical process is known as Hydration of Portland Cement. The addition of water to dry cement powder results in a thin cement slurry that can be easily manipulated and cast into different shapes. In time, the slurry sets and develops strength through a series of hydration reactions. Hydration of cement is not linear through time, it proceeds very slowly at first, allowing the thin mixture to be properly placed before hardening. The chemical reactions that cause the delay in hardening are not completely understood; however, they are critical to developing a rational methodology for the control of cement setting.
Cement mixed with fine aggregate produces mortar for masonry and when it is mixed with sand and gravel it produces Concrete.
Cement mixed with water silicates and aluminates, creates a water repellent hardened mass that is used for water-proofing.
The various types of cement in use today, is the result of many experimentations, testing and improvements made over hundreds of years in order to meet different types of needs. For example, to produce strong concretes for roads and highways, hydraulic mortars that endure sea water and wet climates is required.
Ordinary Portland Cement (OPC)
The rock that is used to create cement is generally limestone and clay. However, it was later discovered that other rock formations provide even more uses for cement. In England, natural rock formations on the Isle of Portland were identified to possess remarkable hydraulic properties. Once water was added to this particular type of rock, it hardened and strengthened even further and it came to be known as Portland.
The most commonly used cement nowadays is this hydraulic cement (i.e. hardens when water is added) called Portland cement or Portland cement blends. Portland cement is suitable for wet climates and can be used underwater. This cement is suitable for all types of concrete construction.
Different types or blends of Portland cement include Portland blast furnace slag cement, Portland fly-ash cement, Portland pozzolan cement, Portland-silica fume cement, masonry cement, expansive cement, white blended cement, coloured cement and very finely ground cement. Each type of cement has its own properties, uses and advantages based on composition materials used during its manufacture.
Portland Pozzolana Cement (PPC)
Portland Pozzolana Cement is prepared by grinding pozzolanic clinker with Portland cement. It is also produced by adding pozzolana with the addition of gypsum or calcium sulphate or by intimately and uniformly blending Portland cement and fine pozzolana.
This cement has high resistance to various chemical attacks on concrete compared with ordinary Portland cement and thus it is widely used. It is used in marine structures, sewage works, sewage works and for laying concrete under water such as bridges, piers, dams and mass concrete works etc.
Blended Hydraulic Cement (BHC)
Blended Hydraulic Cements are produced by blending two or more types of cementitious materials to produce a cement that has better performance. Blended hydraulic cement (BHC) is produced by mixing Ordinary Portland Cement (OPC) and blending materials such as silica fumes, fly ash, limestone and slag to enhance its properties for different uses. BHC can improve workability, strength, durability and chemical resistance of concrete.
BHCs are low heat cements. This makes the concrete to produce low heat of hydration and thus is used in mass concrete construction like gravity dams, as the low heat of hydration prevents the cracking of concrete due to heat.
This cement has increased power against sulphates and is less reactive and initial setting time is greater than OPC. Sulphate resisting cement is used to reduce the risk of sulphate attack on concrete and thus is used in construction of foundations where soil has high sulphate content and in constructions exposed to severe sulphate action by water and soil in places like marshy land, canals linings, culverts, retaining walls, siphons etc.